As optical
backplanes may include splitters, add/drops, star-couplers or
optical switches, the optical power budget must be carefully
managed. Consequently, despite the high power available from
VCSELs, it is highly desirable to minimize the loss introduced
by the waveguide. The value of waveguide propagation loss in
guides should be <0.05 dB/cm at the operation wavelength of 850
nm. Terahertz Photonics have fabricated multimode waveguides
using TRUEMODE Backplane polymer that have a propagation loss of
<0.04 dB/cm. To achieve this requires a waveguide material with
low intrinsic loss and to be able to fabricate waveguides with
smooth surface walls. A scanning electron micrograph of such
waveguide structures is shown in figure 4.
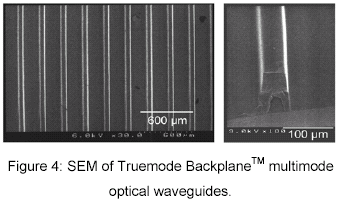
Manufacturability
Truemode Backplane TM
because of its high degree of crosslinking is able to withstand
a high level of punishment during backplane fabrication.
Critical to the characteristics of a polymer for optical
backplanes is that the material must maintain its structural
integrity during lamination to ensure that adjacent copper
layers are not misaligned. The lamination process results in
pressures up to 150-350psi at 180 oC for periods of 1hr. In
addition, the optical loss of the material must not be affected
by the temperature and pressure of lamination or the temperature
profile of solder reflow in which the temperature is cycled up
to 235 oC
during a 160 second cycle. In addition, the extremes of
temperature that a board may be subjected to for sustained
periods during storage and shipping should not alter its
performance.
The adhesion and
performance of the ideal waveguide material must not be affected
by exposure to water. Waveguides should be able to withstand the
‘pressure cooker’ test – immersion in boiling water, and 1000’s
of hours exposure to damp heat- 85% humidity at 85 oC. Such high
thermal and stability and insensitivity to humidity may be
achieved using a polymer such as that designed by Terahertz
Photonics.
The board may be subject
to further post-processing after the embedded guide is
implemented: for example, routing, break-out, drilling of vias,
construction of coupling optics and during assembly the board
will be flexed and put under further strain. The adhesion of the
polymer to the PWB base layer must withstand this without
performance degradation. The polymer developed by Terahertz
Photonics adheres well to both FR4 and copper coated FR4 even
when subjected to damp heat (85% humidity at 85 oC) and
temperature cycling without any surface treatment such as pumice
or micro etching.
If you don't find what you're looking for,
Contact Us.
We may have a suitable product that's not listed, or we may be
able to develop a material to fit your specific needs.
Tel : (02)2217-3442 / Fax : (02)2704-4070
|
|