|
The intricate assembly stage of high value
electronics products brings a number of challenges. The Camera Division
at Sony Manufacturing in South Wales has been researching methods of
reducing a number of assembly-related problems including contamination
from the assembly process itself.
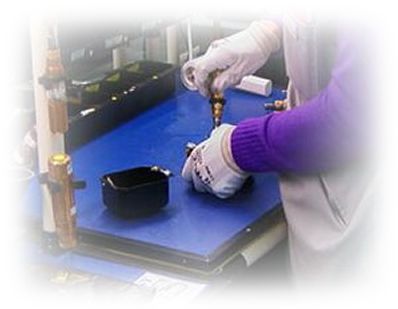
|
|
Sony now uses XBH Non-Slip extensively in
the Camera Division, finding that it has significantly reduced cosmetic
defects by preventing any unwanted movement during assembly. An
additional benefit is that its high tack surface traps particles from
solder and assembly cutting, so that these can then be easily removed
without threat to the assembly. XBH's Non-Slip Technical Manager, Jed
White, says that the Non-Slip material is ideal for electronics
manufacturing.
It can be used in a variety of ways, from
holding small components during cutting and forming processes to
protecting products during final assembly as at Sony. An added benefit
for Sony has been the reduction in the use of protective tape to cameras
prior to assembly; this has saved money in materials but perhaps more
importantly has reduced production time. Non-slip materials can be cut
to the size required and is easily wiped down and de-contaminated using
cleaning fluids commonly used in industry. The material is available in
static dissipative versions too.
|
XBH's range of non-slip materials
provided a number of solutions. With a very high co-efficient of
friction and the ability to hold even the smallest component securely in
place on its surface without the need for adhesives, XBH is gaining
recognition within industry amongst facilities managers whose agenda is
high quality, reduced costs and minimal failure rates. |
|
Electronics giant solves ceramic slicing problems
A major European electronics
company was suffering a high percentage of rejects during ceramic
slicing procedure. The ceramic moved very slightly during the cutting
process, despite the use of a vacuum table. A simple but effective
solution was found with XBH Non-Slip which was perforated to align
with the holes in the vacuum table and was then laid on top of the
table. The result: a dramatic improvement in product quality and yield.
|
If you don't find what you're looking for,
Contact Us.
We may have a suitable product that's not listed, or we may be
able to develop a material to fit your specific needs.
Tel : (02)2217-3442 / Fax : (02)2704-4070
|
|