Plasma is the most
environmentally safe method of both organic removal and surface
modification to date. Plasma processes can be tailored to produce
hydrophobic or hydrophilic surfaces on metals, plastics, glass or
polymers. Recent advances in the uses of polymers and as a result
the need for hydrophilic surfaces for adhesion has fueled the
development of the plasma surface modification industry. This
seminar will review the current industry and how it addresses the
adhesion issue in terms of available equipment and future
potential.
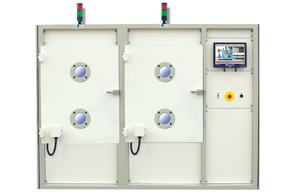
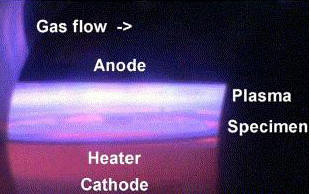
What is Plasma
Plasma can loosely be
defined as a partially or wholly ionized gas with a roughly equal
number of positively and negatively charged particles. It has been
dubbed as the “fourth state of matter" because of its general
properties which are similar to both a gas and a liquid.
There are both high and
low temperature plasmas. High temperature plasma is found at
atmosphere in its manmade form as a plasma torch or naturally in
the form of lightning,.Low temperature plasmas, as used in surface
modification and organic cleaning, are ionized gases generated at
low pressures. These low pressures allow for a relatively long
free path of accelerated electrons and ions which are essentially
at ambient temperatures. With relatively few collisions there is a
low energy transfer thus keeping the temperature of the reaction
in the ambient range.
The ionization of the
gas is accomplished by applying an energy field using one of three
government regulated
source frequencies:
Low frequency or < 100 KHZ.
RF frequency or 13.56 MHZ.
Microwave frequency or 2.45 GHZ.
The frequencies selected
for these sources are controlled by international agreements to
prevent use of sources which would interfere with communication
bands worldwide. Unfortunately for manufacturers, the least
desirable method of generation is
also the least expensive - low
frequency. Low frequency plasmas are the least eflicient
for several
reasons which go beyond the scope of this presentation. The efficiency
is related to the energy necessary to sustain the ionization and
both the intensity and frequency of vacuum ultraviolet (VUV)
radiation.
Most plasma system
use either RF frequency or MW frequency sources.
XBH uses almost exclusively RF sources because of the overall
advantages associated with this
method. RF plasmas have been shown to exhibit significantly higher
levels of VUV which in part explains the higher concentrations of
electronically charged particles than found in the other plasma
sources. RF plasmas have also been noted to be more homogeneous
which is critical in treating irregularly shaped and overly large
objects.
MW source plasmas are
generated “downstream” or in a secondary environment. This means
that the plasma is generated in one chamber and the active species
are drawn by vacuum differential into the work area. Though this
can be advantageous for organic removal it does produce a less
homogeneous process and as a result provides reduced uniformity
across the work area. In areas of surface modification the
effective depth of the modification is tens of nanometers so the
uniformity of the process becomes increasingly important.
There are several
resultant effects to the plasma interaction with the surface, each
of which has a reaction to the adhesion process. These effects
are, but are not restricted to:
Organic removal
CASING (Crosslinking via Activated Species of Inert Gases)
Ablation
Surface chemical restructuring