|
|
印刷電路板 |
|
|
醫療應用 |
|
磁芯上的應用 |
|
|
橡膠上的應用 |
|
|
微電子/微馬達 |
|
|
|
|
|
|
|
|
|
|
|
|
|
|
|
|
|
|
|
|
|
|
|
|
|
|
|
|
|
|
|
|
|
|
|
|
|
|
|
|
|
|
|
|
|
|
|
|
|
|
|
|
|
|
|
|
| |
 |

隨著資訊產業的不斷發展,磁性元件越來越趨向於小型化,3∼5
mm
的軟磁芯、2∼3
mm
的稀土永磁材料,甚至尺寸更小的磁材都不斷被應用。小型超小型磁材的應用,對磁材的防護提出了新的要求。小型軟磁芯作繞線器件使用時,經聚對二甲苯塗敷後能耐1
500∼2
000 V
甚至更高的電壓,由於聚對二甲苯摩擦係數低,繞線操作時將會更滑溜、不傷線、更便於操作。稀土釹鐵硼永磁材料是一種高性能強磁材料,是微型電機小型化超小型化的關鍵材料之一。但是這種材料在空氣中很不穩定,尺寸較大的通常用電鍍或環氧電泳漆作防護塗層,尺寸在1∼5
mm
的小型稀土磁材,特別是環型和筒型稀土磁材,已不能用上述傳統方法實現可靠防護,滿足使用要求。聚對二甲苯獨特的製備工藝和優異性能相結合,使它能對小型超小型磁材進行無薄弱點全塗敷,經它塗敷的稀土永磁材料可浸鹽酸10
天以上不腐蝕。目前國際上小型超小型磁材,幾乎都採用聚對二甲苯作絕緣和防護塗層。
Parylene是非常理想的塗佈塗料,用於鐵芯直徑小於
9.5mm (0.375.英吋)
之產品.Parylene極為一致的塗佈,有著均勻的厚度,即使在轉角和邊緣部份.它是利用氣相沉積的方法塗佈,避免小孔徑堵塞.其附著在鐵芯上的厚度,一般標準約1密爾,增加的厚度微乎其微,同時擁有高阻抗和低摩擦係數(接近鐵氟龍),以降低繞線時線傷.Parylene
其相對導電系數為
2.95,所增加的電容量也是些微.塗佈後的產品可耐1000伏特電壓測試,若要承受更高之電壓,其塗佈厚度相對要增加.
使用Epoxy
環氧樹脂塗佈是用在鐵芯直徑在9.5mm
(0.375.英吋)
以上之產品.大部份利用噴撒的方式達成塗佈.塗佈尺寸約1020密爾高出Paryrlene許多.借塗佈層使鐵芯在繞線時摩擦減緩.及其黏結能力及耐腐蝕的性.,使得鐵芯在老化測試時,保持其功.塗佈後的鐵芯,可耐
1000伏特之電壓測試,若要耐得更高壓,其塗佈厚度相對需要增加.
Parylene Applications -
Magnets & Ferrite Cores
A family of xylylene polymers originally
developed as protective coatings for printed circuit boards are now
finding new applications in areas where other traditional coating
materials are unable to perform to desired specification.
Parylene is the generic name for members of a unique polymer series.
The basic member of this series is poly-p-xylylene, a completely linear,
highly crystalline material. The unique physical and electrical properties
of Parylene, coupled with a stress free application process indicate that
Parylene can be a viable alternative coating option for many types of
material.
Pinhole Free Coating by Vapour
Deposition
Coating is carried out under vacuum and is
best described as Vapour Deposition Polymerisation (VDP). As a coating
technique, VDP offers certain advantages over other coating techniques
such as brushing, dipping, or spraying. These advantages stem principally
from the fact that the solid coating is formed from the gaseous monomer
directly, without an intermediate liquid stage. As a result, the forces of
surface tension, which cause the pulling away from sharp edges and the
filling in of troughs in conventional methods, are not operative. Coatings
of Parylene grow from the substrate surface outward, producing a conformal
layer of uniform thickness. Extensive tests demonstrate that the coating
so farmed is pinhole-free at thicknesses well below one micrometer (1 µm).
Stress Free Application
The Parylene coating is formed spontaneously on components
at or near room temperature; a cure cycle at elevated temperature is not
necessary. The substrate need not be subjected to temperatures above
ambient, and no further time is required beyond that needed for the growth
of the film.
Because the polymerization is spontaneous,
no catalyst is necessary. Catalysts that promote other polymerizations are
often ionic or ionogenic, and, to the extent that they remain in the
coating after cure, their residues are capable of participating in charge
mobilisation mechanisms, with detrimental effects in electrical
properties. Because the coating is formed at room temperature, stresses
that might be induced by differential thermal expansion between the
temperature of cure and room temperature are avoided.
Outstanding lnsulation Properties
In addition to these intrinsic properties Parylenes have
excellent electrical properties, and provide a prime dielectric which has
a low dissipation factor and high dielectric strength, coupled with
excellent mechanical qualities. Such a combination makes Parylene uniquely
suitable for insulation on miniature wire wound components.
The insulating varnish of fine copper wire may be damaged due to the
rigors of the winding operation and particularly in the case of the
smaller devices the toroid or bobbin requires the application of a coating
to not only provide insulation but also to eliminate abrasion damage to
the wire during winding. The high insulation strength of Parylene and its
dry lubricity characteristics make it ideally suited for this
application.
Maximising the Winding Window
The application of Nylon or PTFE coatings tend to reduce the
winding window by build up of these coatings and abrasion protection is
less effective due to surface tension causing thinning of the coating at
edges and corners. Parylene coatings being thinner and evenly distributed
maintain maximum winding window allowing a larger wire gauge to be used
for better performance of the finished product.
Parylene can also be used to "impregnate" wound components and this is
especially applicable to small ferrite transformers and inductors, since
unlike conventional varnish impregnating methods, Parylene does not
introduce the magnetostrictive or permeability problems sometimes
encountered with conventional varnish impregnation. Maximum winding window
is vital for small rotor and stator assemblies. Usually of bonded nickel
iron laminates these components are difficult to coat with Epoxy or PTFE
materials due to the complex shape and retention of coating material
within the winding apertures. Also, due to surface tension, very little
coating remains on the sharp outer corners; the very area where maximum
abrasion to the winding wire occurs. The uniformity of Parylene retains
the window aperture and the full coating thickness on the outer corners
provides protection to the winding wire.
Coating for Miniature Components
The use of adhesive tape as insulation between winding and
metal component is a well established process however as components get
smaller, application of tape becomes difficult, in many instances
resulting in a fall in yield of acceptable parts. A coating of Parylene
can virtually eliminate faulty components plus improving electrical
performance. An excellent example of this is the extremely small bobbins
used as the "pick-up" coil fitted to some Hearing Aids.
Enhanced Strength and Corrosion
Protection
Recent advances in magnetic materials such as sintered and
plastic encapsulated neodymium-iron-boron components, the latter available
in very complex shapes, has highlighted the advantages of the Parylene
coating process. Moulded plastic NdFeB magnetic components are fragile and
an additional advantage of a Parylene coating is increased strength. NdFeB
material is also very susceptible to corrosion from atmospheric moisture.
The extremely low water vapour transmission properties of Parylene provide
excellent protection against corrosion.
Cost Effective Processing
Parylene coatings also offer a reduction in processing and
labour costs since it is possible to coat many thousands of parts
simultaneously using a tumble system during the VDP process which is
analogous to barrel electro-plating. The development of new technologies
as well as the proper utilisation of existing technologies serves to place
new tools in the hands of the engineer and designer which will enable them
to better address today's extremely complex problems.
Liquid
Coating
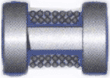 |
|
Vacuum
Deposition Parylene
 |
Liquid
Coatings do not provide even coverage across all surfaces of a coil
form. Build-up of conventional coating material on a coil form can
restrict windings capacity compared to an uncoated form or a form with
a thin and uniform Parylene Coating. |
Thin and
uniform Parylene coating has little effect on the shape and capacity
of a coil form. |
|